Yellowknifers working on their new deck or fence might struggle to finish due to a country-wide shortage of lumber products.
For the city's two primary construction wood merchants, the situation with treated lumber has been a “perfect storm” of high demand and high prices compounded by low supply.
“We started noticing shortages in May. In June it started to become impossible to get treated lumber. It became super scarce,” said Chad Lefrancois, assistant manager of Igloo Building Supplies.
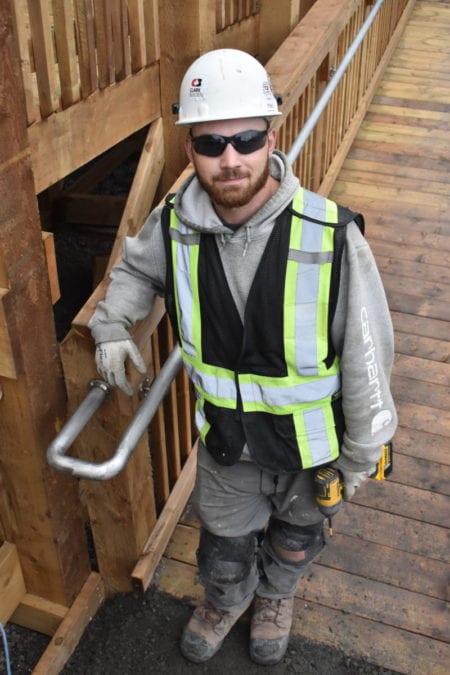
Lumber mill backlog
“The mills were falling further and further behind. They did lay offs, then Covid hit, then they did more layoffs, then just as they were starting to get rolling again the first big flood of orders came in from people who had been at home. (Stores) had no way to fill them. Then the mill stopped giving us arrival times. They were delivering what they could when they could with no projected delivery dates.”
Prices shot up as well, with a standard sheet of half-inch plywood rising to $43.86 from $28.51, where the price stood in early July.
“A 75 per cent increase on the same product in six weeks. That's not common at all,” Lefrancois said.
From his perspective, the effect has been varied. The supply problems haven't affected Igloo's bottom line very much but the ones really feeling the pinch are local builders.
Some have have switched to building their home projects with spruce and then painting or staining them instead of using pressure-treated wood.
Others are opting to put their project plans on hold for a while.
"Their travel budget that changed into a home project budget (because of Covid) might get switched back to a travel budget for a lot of people," Lefrancois said. "My parents in Ontario tried to build a deck this summer but they had the same problem."
Since Igloo relies on their supplier in Edmonton, who in turn relies on mills in Western Canada, there isn't much the Old Airport Road business can do about the shortage.
"Originally, we were told by mid-August they would have it all figured out. But that has come and gone and they're still not able to fill orders normally. So now they're saying mid-September when the demand should go down and they can get back to normal. But, unfortunately, by then our building season will be basically over."
For a contractor like Levi Jones, owner of Side Jobs Contracting and Construction, lumber scarcity has been an issue but it's less of a problem for him because he tends to work on larger projects.
"Any sizable project needs to be planned ahead and materials ordered three to four weeks in advance in order to run according to schedule," said Jones, who launched his company in April. "For us, it hasn't been too bad. The majority of the issue (is with) those looking to get things done quickly on short notice."
Historically unprecedented
Just down the road from Igloo, at Home Hardware Building Centre, owner Chuck Corothers is astonished at the wood shortages that have worsened each month since May.
"In 36 years (of work) I've seen times when pricing went up due to supply restraints but not even close to this," said Corothers, who has worked in Yellowknife for over 26 years and for a decade in Whitehorse before that. He has owned the Home Hardware since 1994.
"The speed the inventory got depleted and the pricing going up, I've never seen anything like this. It's usually very gradual and lasts for a short period of time. Like a hurricane of a massive mill closure, or a rail strike – something like that causes a ripple, but nothing has caused a tsunami like this. It's unprecedented.
"I'm used to ordering and getting told I'll get it in two to three weeks. Now it's two to three months. That doesn't help anybody anywhere," he said.
Corothers explained that when lumber mills in Quebec and Ontario shut down due to Covid, suppliers in the West had to turn to mills in the region just as demand from home-bound families rose.
"And you had Fort McMurray get completely decimated by the worst floods in 100 years. One of the worst hail storms in Calgary taking out roofs and sheeting. It was just pestilence and plague that has continued to make this an issue," he explained.
Corothers gave some examples of items that have sold fast and for higher prices. OSB (oriented strand board) products, which in March sold for $18 per sheet, now goes for $43 per sheet.
One of the most popular wood products, Radius Edge Decking for deck surfaces, sold at volumes four times higher than last year. The store won't receive another truckload until midway through September.
Flexible approach
To cope with the squeeze, Corothers' store has worked to secure supplies from less common sources, and to make the best use of what it has in stock.
“I was sequestered at home talking with every mill I've ever done business with, trying to round up whatever I could," he said, even phoning what he referred to as smaller "grassroots mills" who, unlike larger mills, are less focused on the export market.
His shop has changed its product range, by selling one-by-four-inch pieces of treated lumber instead of the usual one-by-six inches for fencing. And he has sold lengths he wouldn't normally carry, like 20, 18 or seven-inch sheets.
Slow return of market
To a casual observer, it might appear that quick sales of in-stock or freshly arrived products is good for the bottom line, but Corothers said that's not the reality.
"If we can't get the products people need, they'll postpone their projects or won't do them. The cost of the inventory is hard for us. It means more of an investment for each truckload coming in because it costs more," he said. "When prices go up this fast and this extreme it has a tendency to slow things down. We like to see the market strong but steady."
While he's confident prices and demand will eventually settle out next year, Corothers estimates that the mid-term "new norm" will see prices sit around 20 to 25 per cent higher than they were one year ago for lumber, plywood and OSB.
"We're going to be getting a lot of material this weekend. It will be the largest amount of inventory we've had in probably three weeks," he said. "I don't know how long our supplies will last once they arrive."